Saudi Arabia Relies on CTCI for World’s Largest EO/EG Petrochemical Plant
Saudi Kayan 537 KTA Ethylene Oxide / Ethylene Glycol Plant Project
- Market:Hydrocarbon
- Client:Saudi Kayan, a subsidiary of Saudi Basic Industries Corp. (SABIC)
- Prime Contractor:CTCI
- Completion date:2010
- Location:Al-Jubail Industrial City, Saudi Arabia
- Scope of Work:E + P + C
- Capacity:537 KTA ethylene oxide/ethylene glycol (EO/EG)
Driven by strong international product demand and competitive feedstock pricing, Saudi Kayan Petrochemical Company (Saudi Kayan), an affiliate of Saudi Basic Industries Corporation (SABIC) launched an olefins and amines complex within Al-Jubail Industrial City in the Kingdom of Saudi Arabia (KSA). The complex is one of the largest EO/EG plants in the world, and is the key driver of the KSA’s expansion of its petrochemical production capacity. CTCI’s work was crucial as it was the first EPC company to complete the transfer of Care, Custody and Control (TCCC) to Saudi Kayan, enabling the owner to take advantage of the prevailing high price for EO/EG at the time, and providing cashflow to keep the complex’s development on track. The project was an unmitigated success for the owner and CTCI, which completed the TCCC ahead of schedule. The team overcame significant challenges as a result of the unreadiness of utility and offsite facilities, which were being handled by another EPC provider. As a result of CTCI’s excellent overall performance, the team was invited to bid for and won contracts to complete the EPC work of Saudi Kayan’s 210KTA Amine plant and N-Butanol port facilities, both of which were completed in 2012 at the same complex.
The project was instrumental in establishing CTCI’s reputation in the Middle East and helped secure further contract wins in the region. In 2016, CTCI was also awarded two additional contracts at the same facility: the front-end engineering design (FEED) work for an EO/EG debottlenecking plant, and the EPC contract to build an additional cracking furnace that will boost ethylene production.
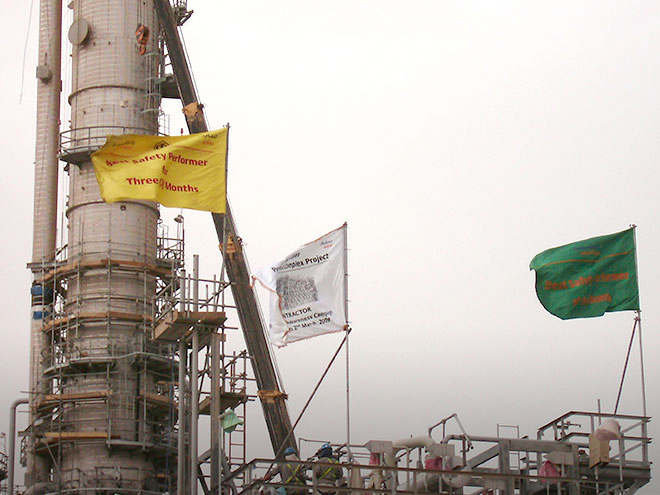
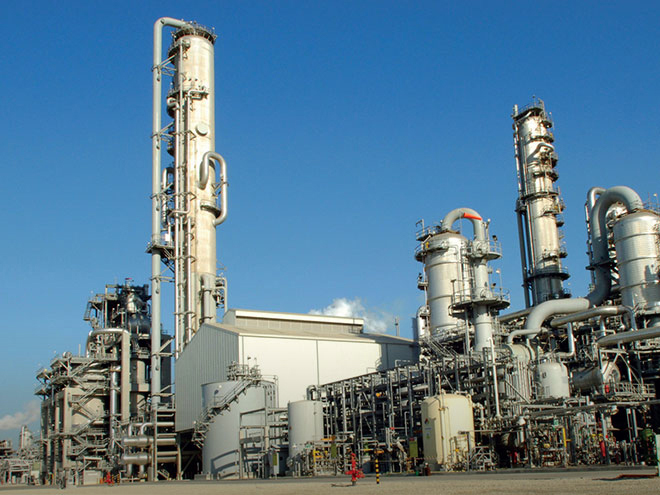
Why CTCI?
Tried and Tested Sub-Contractor Relationships
CTCI beat off strong competition from South Korea's Samsung Engineering Co. and Hyundai Engineering & Construction Co. as well as Japan’s Toyo Engineering Co, as a result of the competitiveness of the EPC LSTK proposal, and a strong track record of designing and managing construction activities in projects across the world. CTCI also had a wealth of experience to offer, having recently completed EO/EG units in Nanhai, China, for a joint venture between China National Offshore Oil Corp. and Shell Co. CTCI’s relationship with Chinese construction sub-contractors was also a crucial factor. At the time, Saudi Arabia faced a challenge due to a lack of skilled construction labor. CTCI was able to solve this problem by proposing to work with a trusted Chinese construction partner, having forged a relationship with them during the completion of EPC work on BASF-YPC’s low-density polyethylene/ethylene-vinyl-acetate (200,000 ton/year each line) project in Nanjing, China, in 2003.
Reliable Realized
Unfamiliar environments, familiar dedication
The CTCI team overcame a series of hurdles that proved their reliability during the project. Initially, they had to get to grips with Shell Global’s Plant Readiness Program (PRP) for Quality, Health, Safety and Environment (QHSE) checking, which had been adopted by the client and was essential for ensuring the safety of the workforce and complex. The client enforced strict conditions on the approved supplier list, with some purchase orders already in place before CTCI joined the project, which the team was flexible enough to accommodate. The technology licensor, Scientific Design, also had serious intellectual property concerns, which meant data and documentation communication was restricted. Despite these challenges, the team completed the project early, working through the intense summer heat to finish the construction work before the ethylene feedstock was even on hand.
CTCI won three of the client’s monthly HSE audits against leading international EPC peers such as Fluor, Technicas Reunidas and KBR to receive the Golden Flag safety award. CTCI hired a 20-strong team of international HSE supervisors and made cash incentives available to all its team and construction sub-contractors to boost performance. The client subsequently invited other sub-contractor teams at the complex to come and learn from CTCI’s example.
Technical Matters
Handling the Heavy Lifting
The primary technical challenge revolved around the sheer scale of the project. The condition of the soil at the complex necessitated work to improve its consistency and prevent accidents during the movement of heavy equipment and facilities. These included a 92.5-meter tall wash tower, which weighed 1,471 tons and required the use of the Mammoet MSG-80 lifting crane, the heaviest onshore gantry crane in the world, and a Liebherr LR-1750 tail crane to erect. Geotechnical investigations established that the site’s ground condition was settlement sensitive and formed by sabkha (salt flat) layers. This necessitated all foundations and structures to be designed to rest on concrete piles, and to transmit loads safely by skin friction. A total of 1,734 piles were cast-in-situ by using the continuous auger method. Steel reinforcement cages were prepared, installed, and reinforced with a concrete-calcium nitrite pour.
Smarter Engineering
Cloud-Served Project Management
At the time of the project, CTCI was already an early adopter of Intergraph’s SmartPlant Materials for project management and documentation control, which allowed for seamless dynamic adjustments between the engineering design and the purchasing, logistics and construction phases of the project. The use of SmartPlant Foundation also allowed CTCI’s onsite engineers to review design and communicate with headquarters in realtime, before conducting a series of model reviews with the client at the 30%, 60% and 90% completion stages, as well as final handover of all the plant project data to the client.
“This project cracked the door for CTCI in the Middle East after an absence of about 20 years.”
Chien-Ming Lin Deputy Project Manager, CTCI